Fostering a Culture of Continuous Improvement:
Implementing the 5S Methodology
Initial Situation: The company sought to improve operational efficiency, reduce workplace hazards, and foster a more organized and safe work environment.
Problem: There were opportunities to improve workspace organization, risk identification, and process efficiency.
Project Objective: Implement the 5S methodology to promote a culture of continuous improvement, optimize workspaces, and ensure a safe environment for all employees.
Solution Implemented:
Regular Meetings: Regular meetings were held with the engineering team to identify improvement opportunities and proactively address issues.
5S Implementation: The five phases of the 5S methodology (Seiri, Seiton, Seiso, Seiketsu, Shitsuke) were implemented in key production areas.
Employee Training: All employees received training on the principles and benefits of the 5S methodology, as well as OSHA safety standards.
Facility Improvements: Improvements were made to the facilities, including signage, safety measures, and equipment organization.
Results Obtained:
Risk Reduction: Potential workplace hazards were identified and eliminated, improving employee safety.
Increased Efficiency: Organized workspaces reduced search times for tools and materials, improving productivity.
Improved Quality: The implementation of 5S contributed to a reduction in errors and defects in products.
Fostered a Culture of Continuous Improvement: Employees actively participated in the improvement process, generating new ideas and suggestions.
Lessons Learned:
Employee Involvement: Active employee participation is essential for the successful implementation of the 5S methodology.
Effective Communication: Clear and consistent communication is key to keeping everyone informed and motivated.
Continuous Monitoring: Regular monitoring of progress and adjustments are necessary to maintain improvements.
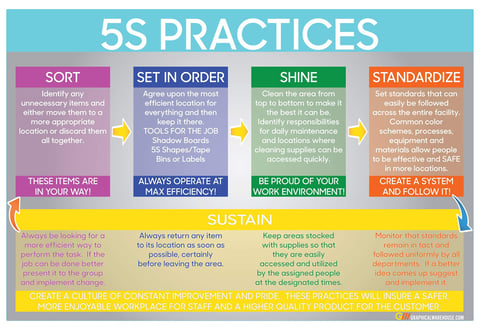
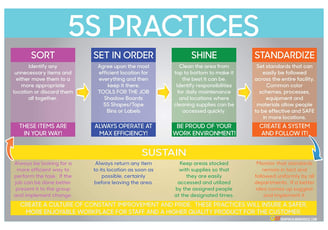